Connectors for medical electrical device OEMs
Dave Bastable, director of business development at Fischer Connectors, has considered how connectors can respond to challenges in the development of medical electrical devices.
The key challenge that OEMs are facing in the development of medical electrical equipment is to keep improving their end-users' experience.
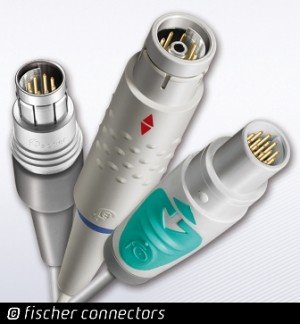
How can connectors respond to challenges in the development of medical electrical devices
This requires reconciling numerous expectations, such as simplicity of use, increased device portability and miniaturisation, while still offering faultless reliability.
Additionally, offering more and more benefits, the specific category of disposable products is becoming more complex.
Finally, the time allocated to OEMs to develop equipment is getting tighter, pushing everyone to streamline product development processes.
Fischer connectors and cable assemblies are primarily known for their reliability.
They are engineered with high-quality materials, fully adapted to medical environments, tested to be shielded against electromagnetic interferences and able to withstand various sterilisation processes.
For instance, we use gold-plated contacts because they are very resistant to corrosion and harsh chemicals often used in hospitals, solid metal bodies for their mechanical strength, or thermoplastics for their heatproof characteristics.
When designing our connectors there are two important parameters we take into account: lightness and compactness.
We have just launched a new series called Alulite, which is typically 50 per cent lighter than typical metal connectors.
This product is ideal for mobile or handheld devices, making them easier to carry and manipulate.
Our ability to offer high pin density and hybrid contact configurations also makes interconnections simpler and less bulky.
In addition, we now integrate embedded electronics into our connectors, which helps to miniaturise cables and add extra intelligence into the connector, such as usage tracking or identification data.
Regarding simplicity of use, the ribbed profile of our connector housings makes them convenient to grip, even with gloves.
The various mechanical or colour-coding possibilities help end users to connect the right plug into the right receptacle.
Plus, our connectors are designed with an integrated locking system, which simply and automatically secures connections without an extra push button or bayonet mechanism.
For disposable equipment, we released a low-cost, high-performance solution called Fischer LUC (limited use connector).
Its key strength is that the disposable plug is mateable with high cycle lifetime receptacles, allowing greater durability for permanent equipment.
To respond to the increasing diversity of needs in disposables, the Fisher LUC is available in many variants, including hybrid-contact or embedded-electronics configurations.
At Fischer Connectors, we attach uppermost importance to customer service.
Our ability to offer complete and integrated solutions combining connectors, cable assemblies and embedded electronics is an asset for medical electrical device OEMs working to a tight schedule.
We can advise OEMs about the connector system that will contribute the most to the success of their application.
Our product range comprises more than 10,000 standard items and we are also able to developed customised solutions.
Access to 3D CAD models and fast prototyping are some of the many value-adding services our customers can rely on.
Not what you're looking for? Search the site.
Browse by category
- Active components (13556)
- Passive components (3584)
- Design and development (10248)
- Enclosures and panel products (3983)
- Interconnection (3643)
- Electronics manufacturing, packaging (3484)
- Industry news (2106)
- Optoelectronics (1959)
- Power supplies (3009)
- Subassemblies (5623)
- Test and measurement (5784)